Implementing Connected Worker at Duravant
Duravant’s Chief Information Officer on the successes and challenges of the Connected Worker program
Add bookmark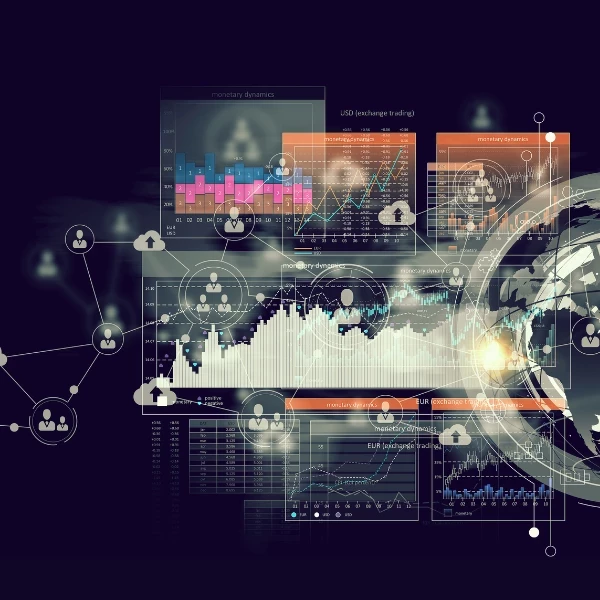
The technology landscape is ever evolving, ushering significant changes for the Connected Worker across varying industries and organizations. With the availability of generative AI and numerous software solutions the industry now has at their disposal, implementation can be challenging, especially across large enterprises like Duravant.
Having acquired multiple companies and businesses over a span of 10+ years, Duravant has established itself as leader in the industry and the manufacturing sector. However, implementing a Connected Worker program across a diverse pool of companies and cultures poses its unique set of challenges and obstacles. Something as simple as harmonizing Microsoft Teams and looking up employees in an “Address Book” across the enterprise poses complexities.
In this interview with Patrick Quint, the newly appointed Chief Information Officer at Duravant, we explore how the company is navigating and leveraging technology to improve their Connected Worker program, and how the company is actively integrating diverse operations and acquisitions into their enterprise to enhance collaboration and efficiency.
Diana Davis, Oil and Gas IQ: What does Connected Worker look like at Duravant?
Patrick Quint: The Connected Worker is important to us, as it is to most companies. For us it means combining hardware, network, and software tools in a way that helps the company communicate across the enterprise. Most importantly, it enables our people to be more productive and share ideas and best practices.
Additionally, there is value to the bottom line by forming relationships, fostering creativity and innovation, and promoting continuous learning within the company. These aspects are critically important for our business.
Duravant is heavily involved in engineering and industrial manufacturing, and we provide services and solutions in three core business segments. Firstly, we focus on food processing equipment in poultry and fish. Secondly, we specialize in packaging equipment for several types of packaging bags and solutions. Thirdly, we offer material handling solutions, particularly conveyor belts, for customers with distribution centers and similar needs. Given the abundance of technical knowledge in these areas, sharing, and collaborating becomes vital for our business.
READ: Enpro’s Journey towards Human Driven Digital Transformation
Diana Davis, Oil and Gas IQ: Is the Connected Worker being used in all those different areas? Are there particular use cases where it’s focused?
Patrick Quint: It’s a bit of a unique situation. Over the 10+ years Duravant has been in business, we’ve acquired 17 different companies and businesses. As a result, we currently have 17 operating companies under the Duravant umbrella, some of which have been in business for over 100 years.
These businesses have their own processes, tools, and methods of communication that have been effective for them until now. Our challenge is finding the right balance of achieving synergies and implementing centralized standard processes and data sharing, while also allowing each company some level of independence to excel in their area of expertise.
Being appointed Chief Information Officer just two months ago, this is the landscape I’ve inherited. I’m in the process of understanding our current state and where we need to be. It’s clear that there is a need for effective communication. For us, that means focusing on fundamentals like enabling people to look up other people in the address book, using O365 tools effectively, simplifying administration, etc. at an enterprise level.
While many companies may not face these challenges, due to our acquisitions, we need to establish effective guidelines for even using Teams and Office 365 tools. These are the areas we are actively working on and believe will make a meaningful contribution to our progress.
Diana Davis, Oil and Gas IQ: Has there been an evolution of the Connected Worker?
Patrick Quint: Prior to my arrival, the company was experiencing rapid growth, acquiring numerous companies and businesses. The focus then was on incorporating those businesses into the overall enterprise. Many of these companies have been operating independently for years and in many ways, still do.
However, we recognize the need to change the culture around information sharing and understand how open the teams are to knowing what other businesses are doing. We are seeking ways to integrate our solutions and share best practices to establish common processes and reduce costs.
As the champion of the Connected Worker, I am looking at ways to improve our solutions, network, and infrastructure backbone to meet business needs across the entire enterprise. Over the last couple months, I have seen a significant change.
LISTEN: Westlake Chemical's Digital Transformation Journey
Diana Davis, Oil and Gas IQ: Working across so many different businesses, it’s evident that you’ve got your work cut out for you. What technologies are you looking at to support this?
Patrick Quint: There are several technologies at play, ranging from hardware and software to network infrastructure. At the most basic level, we are focused on consolidating Microsoft tenants.
Currently, we have 10 Microsoft tenants in our business. This means that it’s nearly impossible to look up someone is another tenant, find their contact information, or send them an email. In internal Teams meeting, employees in different tenants are treated as guests and must be added into meetings hosted by another tenant. Using SharePoint or other sharing platforms is also not seamless when dealing with multiple tenants.
Additionally, from a security standpoint, we need to implement a single sign-on process for all our major applications to improve the user experience.
Consolidating our Microsoft tenants is our current top priority, and the project is already underway. Once we get there, it will open the door to many other possibilities. We will be able to fully utilize the Office 365 tools beyond current limitations. We’re also harmonizing other solutions like Salesforce across the enterprise, enabling everyone to use the same tools and follow the same processes.
Regarding processes and procedures, we are focusing on ERP consolidation. Streamlining our ERPs into two standards will improve data management and processes. Establishing the right enterprise data and analytics platform in the cloud will enable standardized data flow, easy access to information, and better data driven decision making.
It is astounding how challenging it is to establish basic foundations. Most of it comes down to culture – changing the way people have worked in the past, which is a significant aspect of the Connected Worker concept. To change people’s behaviour, you are employing communication channels and organizational change management techniques. We explain the reasons behind the changes and emphasize why it’s better to work differently. It’s important for individuals to understand that while they were succeeding within their independent companies, we now need to succeed as an enterprise.
Diana Davis, Oil and Gas IQ: What are some examples of how you're addressing the cultural issue? I can imagine it’s a challenge given the diverse cultures within the organization.
Patrick Quint: There are many tools out there, such as those provided by Office 365 – Teams, Power BI, SharePoint, OneDrive and more. Our focus is to ensure that for every tool we introduce, people understand the business scenarios in which they should be used, and which tool is effective for specific solutions.
We communicate via various channels, providing tips and techniques. We organize ‘lunch and learns,’ distribute newsletters, and try different approaches to help our employees understand. Furthermore, we only deploy tools that have a purpose and are ready for use to minimize confusion.
LEARN: What is Connected Worker Technology?
Diana Davis, Oil and Gas IQ: What have been the biggest challenges so far?
Patrick Quint: The biggest challenge lies in alignment and organizational change management. Each company has its own president, all of whom want what’s best for their respective company. Moreover, each company has its own perspective on what’s best for the overall enterprise based on its individual needs and priorities.
Hence, the challenge is in vetting and understanding which tools hold the greatest value proposition for the entire company. That involves a well thought out strategic plan. The most difficult part is staying focused and to avoid distractions.
Diana Davis, Oil and Gas IQ: How do you measure success and ensure that you are on track?
Patrick Quint: As with any initiative, there must be a business value proposition in place when implementing something. In the case of Connected Worker, there are specific indicators I look at. For instance, when we deploy a tool like an Office 365 application, we assess whether people are using it for the right business scenarios. We monitor usage statistics and observe whether connections are forming across the operating companies. This indicates information sharing and cross-functional collaboration.
We also gauge success through our service desk. We monitor the kinds of questions/tickets that come in, such as inquiries about tool usage and connecting with other groups. We consider the frustrations that arise and use that to guide us on what steps to take next.
I meet with all the presidents on a regular basis to understand their opportunities and challenges and how technology can help enable their business plans. Those interactions help us determine if we’re on the right track.
Diana Davis, Oil and Gas IQ: How do you see generative AI impacting Connected Worker? Is this something that you're already thinking about for Duravant?
Patrick Quint: AI language models are a real game changer. Everyone needs to be aware of their impact, or risk being left behind. In the past, data scientists possessed unique skills to analyze large volumes of information and build models. However, now with generative AI, the common worker can access and utilize that kind of information. It has democratized this capability, making it easy for everyone to become a technologist.
Currently, most people, including myself, are still learning what generative AI can offer. We need to identify the uses cases that make sense from a business perspective rather than seeing it as cool tool to experiment with. For example, it can save time with creating a job description by prompting AI with the right questions. Businesses should closely examine possibilities like these.
From our standpoint, we aim for a balanced approach. We want people to have the ability to leverage generative AI capabilities embedded in search engines and software-as-a-service (SaaS) products. At the same time, it is crucial to establish security measures and policies to prevent confidential and propriety information being uploaded into these tools. We are currently communicating these guidelines to our employees.
While we want to enhance productivity and encourage learning, we must also protect company assets. It’s a journey we’re undertaking, and it includes educating our executive teams about the potentials of generative AI. Being prepared is essential.
READ: How Shell is Evolving its Digital Twin to Drive Business Value
Diana Davis, Oil and Gas IQ: What would be your advice to somebody who's looking at starting a Connected Worker implementation or journey?
Patrick Quint: It is essential to have a comprehensive understanding of your enterprise and your workers. This requires effective communication. Identify the barriers that need to be broken and provide workers with the tools, frameworks, and guidelines to solve problems in ways they deem most appropriate.
Gather as much information as possible from different stakeholders within the enterprise, prioritize based on themes, and use a steering committee or governance committee to vet areas of Connected Worker that offer the greatest value and impact. Once you have a solid plan and the necessary resources, focus relentlessly on the execution and making a difference. Do not let distractions slow you down.
Diana Davis, Oil and Gas IQ: Final question! What are you looking forward to at the event?
Patrick Quint: A number of things! I’m always interested in hearing what other approaches and strategies have been effective for different people and their organizations. There’s always new tips and techniques to make Connected Worker more effective. Sharing some of our journeys with other peers is quite helpful.
The complexity of our landscape is being decentralized, but at the same time, we’re trying to figure out certain aspects to get the most out of our workers. I’m looking forward to sharing that and learning from other people about what is or is not working for them.
Interested in learning more?
Patrick Quint will be speaking at the Connected Worker Summit in Chicago this November. Download the agenda and join over 300 technology and operational leaders for a cross-industry exploration of the challenges faced by digital manufacturers, and understand how they can better connect workers to the resources they need to do their work more effectively.