How BP and Chevron Use Digital Twins to Optimize Assets
Add bookmark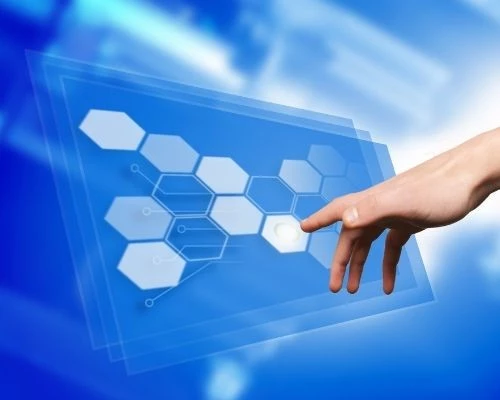
Leading oil and gas companies have been using digital twins for years to accelerate production, reduce operating costs, minimize risks and improve decision making around asset maintenance and operation.
A digital twin is a virtual representation of a machine, process, or other physical object. It relies on real world data to accurately represent how a process or object behaves.
Digital twins have become increasingly sophisticated and accurate with advances in artificial intelligence and machine learning.
“By replicating an asset or a portion of it in the virtual world, companies can run simulation tests on real-world problems and visualize the results in 3D,” comments Ravindra Puranik, Oil & Gas Analyst at GlobalData, commented in an article.
“This is helping project engineers to improve their understanding of the asset, thereby enabling them to optimize its performance as per the market requirements. Thus, digital twins are gradually becoming integral to oil and gas operations.”
Here's how two leading oil companies are using digital twins.
BP
BP began rolling out its digital twin across its production systems globally in 2017. The company says that the digital twin has been instrumental in helping engineers to optimize assets and identify potential issues before they arise.
Optimization analysis that used to take more than a day, for instance, can now be performed in 20 minutes, according to BP. This drastically speeds up the time to insight and frees up valuable engineering time.
The company was able to produce an extra 30,000 barrels of oil in 2017 the first year of their digital twin implementation.
More recently, BP has been digitally transforming operations at Argos, its floating production unit, at the Mad Dog field in Green Canyon Block 780. In the unit, the company has implemented what it calls a “dynamic visual twin”.
According to an article publish last year in Upstream Online, the twin integrates real time data and shows all aspects of the unit’s operations. By making use of machine learning, the system can alert human operators to changes over time – in the case of corrosion monitoring, for instance – that may merit further investigation.
Ken Nguyen, Principal Portfolio Manager at BP for the project, says in the article that the system is designed to take care of routine tasks so that “facility staff can focus on high-value tasks that require a human touch.”
He adds that BP is also using the dynamic visual twin as part of its training program. New recruits don Microsoft HoloLens smart glasses and practice the routine tasks that they are expected to know before they’re sent to the offshore environment.
“They're able to turn a wrench here or operate something there and the assessor can see if the person is ready to go offshore,” he explains.
“Fundamentally, it's changed the way we approach the integration of various technologies, such as the digital twin and the use of a mixed reality like the HoloLens. It allows us to be more immersive and to do things onshore and not have to go offshore."
Chevron
Chevron has been integrating a range of digital tools into its operations from old oil fields to new natural gas projects. The company says that its investing billions of dollars “strengthening its base business, keeping [its] new assets on line and growing production.”
Improving reliability is one of the keys to ensuring optimum output. Chevron says that this includes “involves advancing and automating our operations by using existing, emerging and yet-to-be-developed technologies and workflow enhancements. It involves generating better data that our software can convert in real time into useful information – enabling us to operate more safely, reliably and efficiently; reduce costs; recover more resources; and better manage risks.”
According to Abe Eshkenazi, writing for the Association for Supply Chain Management (ASCM), Chevron is using digital twins for predictive maintenance in its oil fields and refineries and aims to incorporate sensor data from most of its high-value equipment by 2024. The company expects that preventing breakdowns could save millions of dollars each year.