How Chevron Canada is Driving Operational Excellence to the Frontline
An interview with Troy Geertsen, Vice President, Health, Environment & Safety at Chevron
Add bookmark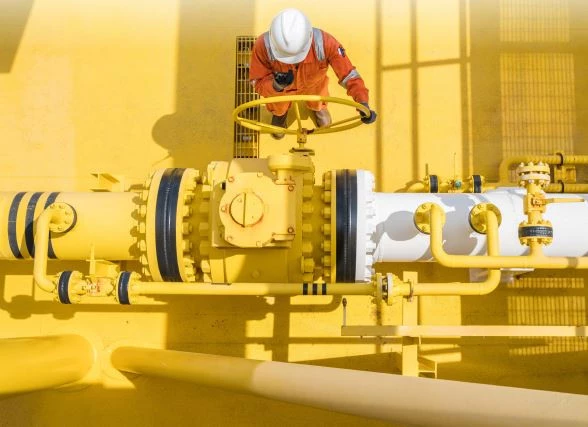
Troy, tell us about your professional background leading up to and including your current role at Chevron Canada?
I started my career in the late 1980s on the regulatory side of the upstream energy industry with the then-called Energy Resources Conservation Board in Alberta. I worked as a field inspector where my role included inspection of environmental events, facilities, pipelines, drilling and service rigs and responding to public complaints. I was very fortunate to get a well-rounded experience in the upstream early in my career.
I was always interested in both the regulatory and the operations side of the upstream industry, so I transitioned to medium and small exploration and production organizations supporting compliance, safety and environment performance. I learned a lot in these positions, as operational excellence was being talked about at higher levels within the industry, but the culture was not always obvious in the field. It was my job to help communicate the OE message to frontline workers and supervisors and build the OE culture. I supported the drive to understand the risks associated with our business and worked to ensure we had safeguards in place. Unfortunately, during this time we sustained some very serious incidents, including a fatality, and, in some cases, repeated this level of performance. It got me thinking: although we were a relatively mature industry, we are still experiencing serious injuries and fatalities and sometimes accepting this performance – there had to be more that we could do. At the time, we struggled with becoming learning organizations.
Eventually I was asked to support an early-phase LNG project on Canada’s east coast. At this point in my career, it was exciting to work on a major capital project that, if successful, may result in new energy streams in Canada.
Then I transitioned to Chevron supporting major capital projects in the oil sands, deep water Gulf of Mexico, Nigeria and a new country entry into Liberia. This included supporting OE for large production platforms, including engineering/design and construction to hook-up and commissioning. We also supported environmental assessments, Metocean studies and offshore drilling work. We were responsible for ensuring required risk management and environmental processes were in place and executed and that our diverse workforces were supported in fabrication yards and offshore.
Over three years ago, I was asked to return to Canada in the role of Vice president, Health, Environment, Safety and Regulatory for our Canadian operations. Overall, my team is responsible for stewarding Operational Excellence and driving to world class OE performance.
How does Chevron define Operational Excellence?
At Chevron, there are several focus areas that fall into our definition of operational excellence including workforce safety, environment, process safety, efficiency, security and stakeholders.
The efficiency piece is interesting, and we are starting to explore what that really means from a Canadian perspective. As we start exploring technology and implementing digital solutions within our organization, we begin to open the door to becoming more efficient.
When it comes to safety and risk management, what are you doing to drive operational excellence to the front line?
Until recently, Chevron’s operational excellence management system was focused on doing everything, all the time – something that we now realize is impossible. We executed all OE processes and procedures in the same way across the company. We audited almost every requirement, regardless of the level of risk involved, and operated like that for years. Don’t get me wrong: we needed to develop this OE culture at the time to start moving the needle; now we need to focus on the higher risk work.
We were doing all this work, but we were still having fatalities globally. Based on historical data, we could anticipate having three to five fatalities within the corporation every year. We found that our recordable incident rate, specifically low-consequence events/injuries, was trending downward and approaching world-class levels. However, our fatality rates were going up. Our management system was forcing us to do more work on the low-consequence side and not allowing us to focus as much time on the high-risk, high-consequence events.
Two years ago, Chevron commissioned a multidisciplinary team to review and update our OE management system, and as a result we now have an updated OEMS which is risk based. We now focus our efforts on ensuring we have a better understanding of the risks associated with our operations with the management system tailored to mitigate those risks. As an example, if drilling a well is a business unit’s highest risk, then we are going to focus our management system on the highest risks of drilling and make sure safeguards are in place and functioning. It’s about getting back to the basics and understanding what could seriously injure people or cause a significant event. We believe this shift in our management system is an important element that helped us sustain a fatality-free year in 2018 – the first in the corporation’s history.
In addition, we commissioned another multidisciplinary team to review our serious incidents over the last seven years to figure out what really caused these fatalities. They discovered some really basic procedures that we needed to change. Our systems had grown to be so complex over the years, with on-site paperwork and other reviews, that people were drowning in process and paperwork and not truly understanding the hazards or ensuring key safeguards were in place to mitigate the risk.
To support this shift, the team developed Save Your Life Actions and Start Work Checklists for our field workforce. Before starting any job that involves a critical task, workers complete a start work checklist that contains five or six critical safeguards and then verify those safeguards are in place. It’s Safety 101. It’s about understanding the hazards, verifying the safeguards are in place and making sure the team is engaged. The checklists are basic. If we do everything right according to the nine start work checks (different work scopes), we would have reduced our number of fatalities by about 30% to 40%. They have clear instructions and diagrams. They were designed for the workforce, not for supervisors or auditors.
This is the beginning of our fatality prevention initiative.
How are you encouraging practical and effective field conversations - and how can you embed those conversations into your organisational DNA?
The Start Work Checklists are helping us with these conversations, but we are also embracing human performance concepts. People inevitably make mistakes. When things go wrong, instead of overreacting, we’re trying to figure out what may have caused the individual to make that mistake. We are doing this in a positive way, not in negative way focused on accountability. Although we are still early in our human performance journey, we are starting to see benefits.
Human performance teaches us how to ask the right questions to better understand why errors or incidents occur. What were some of the latent conditions? Maybe an individual was told to do something incorrectly for many years and the person felt this was the normal course of business? Is that the individual’s fault or can it be attributed to the underlying conditions? Is the individual having difficulties at home which may have contributed to the mistake?
We are now starting to drive human performance conversations down to the worker level. We have communicated the concepts with our leaders and supervisors.
Ideally, we would like to get to a point where small crews on-site can feel comfortable enough to put up their hand and have conversations like, “Hey, am I not feeling well today? Is my head in the game?” I know we have a long way to go, but that’s the conversation we’re trying to drive.
You often discuss how Chevron is developing into a better learning organization. Can you elaborate on that?
I think we are on our way to becoming a better learning organization. Most organizations are diligent at sharing detail of an event or actions, but we’re not good at taking those lessons and implementing them into future work.
For us, becoming a learning organization means we are not just about learning from failures, but also learning from our successes. We want to look back at a successful job and bring those concepts into our next project. It’s difficult because we always want to analyse the things we can improve on, but then we miss out on learning from our successes. We’ve started initiating learning team concepts from our downstream organization to start having this conversation.
If we have a challenge or problem at the field level -- for example, maybe a valve failed that resulted in a loss of containment -- instead of conducting a formal investigation, we establish a team with the right experience at the field level. The facilitator is a peer and the group need to have a discussion without consequence – meaning they are open and honest. They talk about how the work is really being done, regardless of what the procedures states. With the support of supervisors and managers, the team meets and within a short period of time develops practical solutions to the problem.
The key here is that when the team determines actions at the field level, leadership respects their input. If the respect is not there, the learning team doesn’t work. There are some real benefits to moving away from formal investigations and focusing on the people and how the work is being executed. We have seen great success in our downstream operations, so we will be implementing the learning team concept in our upstream operations in 2019.
How is Chevron Canada leveraging new technologies to enhance field operations and worker safety?
Chevron recently conducted a study that found we were lagging our peers when it came to technology and digital transformation. Since then, we have opened a global conversation about digitalization and it’s become a core initiative for us in 2019 and beyond.
We are looking at everything -- from how we manage our paperwork to how we use artificial intelligence in the corporation. There are many existing technologies and solutions that we can adopt right now. We are working on changing our culture to allow that to happen. If we don’t move forward with digital transformation, we may not see the performance results we need as a corporation.
When it comes to worker safety, we have implemented lone worker wearable technology. Our Canadian field workers are wearing technology that can monitor their movement by satellite or cell phone. The technology not only monitors worker locations for emergency situations, it also monitors atmospheric conditions, or if a worker falls on the job, etc. Also, the technology requires workers to respond throughout their shift and confirm their well-being. We are working on a dashboard to manage this data to support a connected worker concept.
Your role at Chevron Canada isn’t only focused on safety. Can you share some of the initiatives that you’re working on to improve the company’s environmental performance?
Two of our primary environmental concerns in Canada are air emissions and water use. We have a lot of fracking in our operations, which requires a large volume of water. As we move into development activities in our Kaybob Duvernay asset, we are reviewing technologies that allow us to recycle and reduce water consumption with our peers on technology solutions. Even though the industry can obtain approval for water use, our stakeholders, the public, are still concerned about the impact of our operations, which we take seriously. We are accelerating our focus in the space and we will continue to invest and adopt new technologies to reduce our water use.
Technology solutions are also being applied to reduce emissions in all our new facilities. We are moving towards using chemical pumps and chemical systems that don’t have any emissions, which may also reduce the likelihood of spills and reduce operating costs, thus allowing us to become more efficient
In your opinion, what is one or two things that companies should focus on to become operationally excellent in the areas of environment, health and safety?
Frontline supervisors must buy in to key OE concepts and understand how leadership with human performance drives OE performance. It’s not about hiring more HES people to monitor and audit. It’s about getting the right people with the right leadership who are open to trying new ways of doing business. If companies can get that under control, and align themselves with the right business partners, they will be on the right track.
Like most upstream organizations, about 95% of our capital dollars are executed by business partners. In 2016, we developed a high-level operational excellence strategy, part of which was focused on building better relationships with business partners that align with our strategy. One of the key aspects includes meeting on a yearly basis with the senior leaders of our business partners that conduct high risk work to talk about operational excellence. It’s just a conversation between three or four senior leaders. As we conduct these engagements, we are experiencing much better alignment with our business partners year after year.
Our industry has been diligent about telling people what to do and how to do it; however, we have not been good at telling people why. People learn better when they understand the why versus the what. In our experience, you will get better buy-in when you make OE performance personal versus something you do because your company or supervisor says to do it.