Four Workforce Management Trends in Oil and Gas
Add bookmark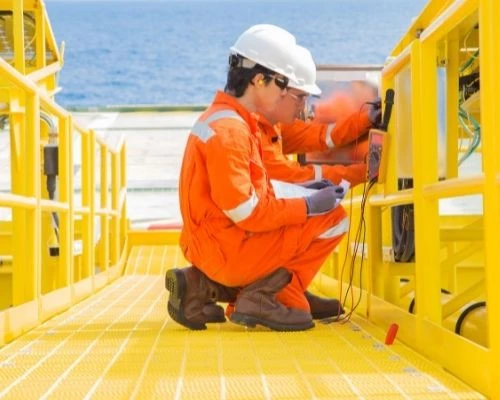
With an oil price that has swung down and up almost as fast as you can say bitcoin, it’s an understatement to say that it’s been a tumultuous few years for the oil and gas industry.
To some extent, digital technologies have helped oil and gas companies manage the turbulence by enabling new ways of operating that increase efficiency, reliability and production while simultaneously reducing costs. These new technologies are dramatically changing the way the industry operates by improving everything from machine diagnostics and maintenance to offshore drilling.
Technology enables oil and gas companies to maintain operations with fewer staff. But it is also having an impact on the types of required jobs and skills.
Last month, Oil and Gas IQ assembled executives from across the oil and gas supply chain in Houston to discuss how automation is changing their business needs and approach to workforce management. Here are four key trends that they identified.
#1: Repetitive work will continue to be automated away
While automation is nothing new, the development of more advanced data analytics, machine learning and artificial intelligence is enabling companies to automate new processes and operational areas that were previously too complicated to touch. Back-office functions were seen as highly susceptible to automation.
While automation has the potential to lead to redundancies, all the panelists were quick to point out that people could be reallocated to new areas of the enterprise and helped to develop new, more relevant skillsets.
“As leaders we need to help people to see what their future with the company is. We’re going to find opportunities for you,” says Sean Barnes, VP, Operations, Nine Energy Service.
Workers can also benefit from automation in terms of improved conditions, says Andy Cuthbert, Global Prevention, Relief Well Engineering & Technology Manager, Halliburton.
“By introducing automation into the offshore industry, we can reduce risk, we can have fewer people manning the rigs; changing the working conditions so they don’t need to be away from home for so long,” he says. “The Industrial Revolution didn’t decrease workers’ wages; it actually increased them and improved their working conditions.”
Technology can free up valuable staff time by automating mundane tasks to leave staff free for more specialist and knowledge-intensive work.
#2: Need for new skills – especially in data and digital
As certain jobs are automated, new opportunities will emerge that require new skills. Automation and digital initiatives, for instance, have intensified the amount of data being produced at oil and gas companies. That data has the potential to provide enormous insight into business operations – but only if you can use it.
“The more data we can extract, the greater our expertise,” says Halliburton’s Cuthbert. “[But that means] the more we need people who can process this data – to interpret it and use it.”
At BP, according to Ken Nguyen, Digital Program Manager, this has meant embracing digital across every part of the business. “[We had to] upskill every part of the organization in digital skills. […] We had to find the gaps, do the assessment and help our staff.”
It’s not just digital and data skills that have been increasing in importance as automation and new technologies bring new ways of operating. Interpersonal and problem-solving skills are increasing in importance – and need to be more highly prioritized.
“Hard skills are going to continue to become commoditized and automated away,” says Sean Barnes, VP, Operations, Nine Energy Service. “Soft skills are now superpowers. We need to start having more conversations about how we build teams and leaders that understand the importance of soft skills.”
Deana Werkowitch, SVP- Audit, Technology, Implementation Services, Crestwood Midstream Partners, agrees and says that she feels the term ‘soft skills’ devalue how important these abilities actually are.
“When you’re thinking about automation when you’re thinking about tools, the skills we really need can’t be replaced by machines,” she says. “It’s the way we communicate. The way we critically think. The way we innovate outside of a machine.”
#3: Training becomes more immersive and embedded in the flow of work
Training for highly technical assignments used to involve extensive amount of classroom-based education. But the oil and gas industry has embraced virtual reality and other digital tools to help better support workers hands on training that will be more relevant and remembered than a class-based approach.
Virtual Reality now plays an enormous role in many training programs. Workers can experience no risk, simulations before confronting the real-world equivalent. Not only is this approach safer but it is also more likely to be retained.
“Where we want to move to is a more immersive type of training,” says Halliburton’s Cuthbert. “We want to immerse ourselves in a situation so it becomes more like muscle memory.”
It’s an approach that resonates with BP’s Nguyen.
“The way that we educate people has fundamentally changed. A lot more hands on experience, work as you go and supplant the training as you need,” he says. “We find that using things like YouTube and social media is the way that people learn want to learn and the way they learn best.”
This virtual and on demand approach to training can help to save unnecessary costs as well. Nine Energy’s Sean Barnes says that instead of renting a crane to enable operators to get their crane certification, for instance, they can now be sent into a VR World that is just as realistic.
#4: More outsiders will be hired into the industry
The traditional model of oil and gas companies was to grow and nurture talent from within. The business requires a high degree of specialist knowledge and extremely complex operations.
However, as the industry shifts to require fundamentally new skillsets and existing workers retire, oil and gas companies are being forced to look outside for new recruits.
A survey published last week found that nearly half of oil and gas workers expect to leave the industry within the next five years, for instance. That comes at a time when the industry is already struggling to hire skilled workers to run its operations. Unless they can attract new talent from outside the industry, oil and gas companies will struggle to fill many roles.
“It’s the chicken and egg,” says Halliburton’s Cuthbert. “You can either grow people organically from the inside or when you bring people in from outside, then they have to have the knowledge about where the industry is going to be in 20 years.”
BP’s Ken Nguyen says that there are advantages to recruiting people from outside the oil and gas industry.
“We’re injecting new ideas and skills that changes fundamentally how we approach old problems,” he observes. “And that’s quite refreshing."
Interested in Learning More?
Having frontline workers that are safe, connected and empowered to make intelligent, informed decisions is the number one way to build resilient operations. Join us at The Connected Worker Summit on May 3-5, 2022 and network with over 200 operations leaders at the Norris Conference Center in Houston, TX. Learn how to build a connected workforce to improve operational efficiency, training, asset management, quality, and safety. The Connected Worker Summit (oilandgasiq.com)