How High-tech Helmets and Huddle Boards Drive Efficiency at TotalEnergies
Add bookmark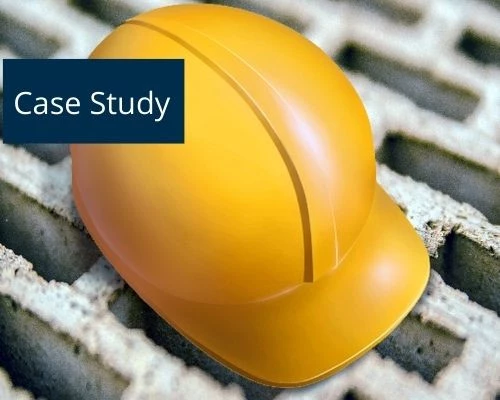
The first time that Blake McFall saw a RealWear connected helmet, he was at home. His company, TotalEnergies, had shipped them from France directly to him. The helmets were to be trialled to help troubleshoot machines and maintenance at the company’s polypropene plant in LaPorte, Texas where McFall is Maintenance Manager.
“I put it on and 10 minutes later I was an expert,” he said, noting that the helmets were incredibly easy to use. “The first thing we did was inspect my garden in the backyard!”
Garden inspections were not exactly on the list of intended uses for TotalEnergies' connected helmet. The helmet allows workers to connect remotely to subject matter experts. An eye piece and video camera allow an on-site worker and remote assistant to communicate and view the same information in real time.
Noise cancelling headphones and an integrated microphone make it easy to talk, even in noisy environments.
It is a big improvement over the way things used to be done, explains McFall, speaking at Oil and Gas IQ’s recent Connected Worker conference in Houston.
He says that before the introduction of the connected helmets, a mechanical issue would often result in a phone call to the technical group in Europe. Since there is a time difference, it would usually take a day for technical staff to get back to them.
The team would then need to locate and download various documents and schedule a meeting for later in the week. If that meeting didn’t resolve the issue, a subject matter expert may need to get on a plane and come to the plant.
The helmet eliminated those processes and enabled workers to troubleshoot machines quickly and with a higher degree of accuracy.
“You can connect the expert with the man in the field directly,” explains McFall. “[They are] able to see. Able to hear.”
Field workers can access visual information and documents about procedures and machine specifications eliminating the need to carry paper procedures into the field and keeping hands free for work. The helmet integrates with MS Teams so that workers may collaborate with others using a platform that everyone is already familiar with.
WATCH: The Connected Worker Maintenance & Inspections
TotalEnergies has now rolled out the helmet globally with around 100 helmets in use at various facilities. He says that the company has used them for training purposes during Covid lockdown in Belgium, for rebooting a catalytic injection system at a refinery in France, and for inspections on barges in their upstream division.
At the LaPorte plant, McFalls says that workers use the helmet regularly and it is especially useful during shutdowns and turnarounds.
The connected helmet is one example of how wearable technology is transforming operations in heavy industries such as oil and gas.
Wearable technology – which includes helmets, eyeglasses, watches, “smart fabrics” or other devices that workers can wear – helps keep workers safer, access information and support directly in the field, and conduct essential job functions more efficiently.
Industrial environments are becoming connected ecosystems where humans and machines are connected to the internet via sensors that can monitor the health of both person and machine.
Temperature and vibration data on a machine, for instance, could indicate an impending fault on a piece of equipment. Heart rate data on a person could indicate a level of fatigue that make it unsafe to continue in certain environments.
READ: 6 Technologies Redefining How Energy Companies are Managing Worker Safety
“Digital helps us bring that efficiency to our current operations,” says McFall. “Higher reliability of equipment means less time on little value-added items. That adds up to meeting an inspired workforce.”
The other innovation that McFall has implemented at the LaPorte facility is the use of digital huddle boards, an extension of their Lean Manufacturing program.
He explains that when they first started rolling out Lean, they were physically sticking post-it notes on a board. When it came to tracking KPIs, an engineer would make the rounds every day and collect data.
But, explains McFall, the company realized that was not the most efficient process and wanted to digitize it.
The result was a digital huddle board, which was a tool to keep track of key performance metrics and visualize workflow.
The board was built in-house using Microsoft’s Power BI and they implemented it on touch screens. The screens are connected to a camera so that people in the control room can see the same KPIs and tracking information as workers in the field.
“[Workers] can see exactly where we stand today as an organization,” says McFall. “That was very empowering for them.”
The digital huddle board concept started with one screen and has now expanded to nine at the LaPorte facility.
Key to the success of both installations was the fact that they were low-cost innovations that were easy to use and brought benefit to workers. McFall says decisions such as sticking with MS Teams for the helmet and using a touch screen for the huddle boards were key to ensuring that the frontline found the tools easy to use.
Connectivity was another challenge that they had to overcome in the implementation process. Some areas where workers had to operate did not have adequate connectivity to support the use of the helmets. McFall says that they had to “triage” and prioritize connectivity in areas with the highest impact first.
As Total seeks to find new ways to drive a value-driven culture, McFall says that they will continue to look for ways to empower their frontline through digital innovations.
Interested in Learning More About this Topic?
Join over 200 industry leaders on 15-17 November 2022 in Chicago at The Connected Worker conference to learn how to build a connected workforce to improve resilience, agility and growth in a recovering economy. Hear case studies from leading organizations and learn about trailblazing technologies that will transform your operations. Download the agenda here.