How Chevron, Marathon, and ExxonMobil Embed Operational Excellence
Add bookmark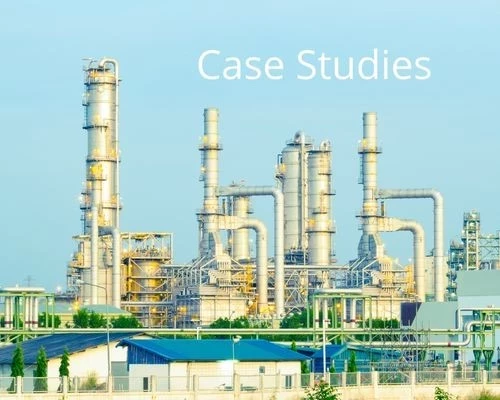
With increasing speculation that the next oil price downturn is just around the corner, oil and gas companies are under immense operational pressure to drive efficiencies and improve business performance.
They are suffering from both the loss of human capital following the COVID-19 pandemic, and the long-term industry labor trends that has seen the retiring of large numbers of skilled, technical workers.
They are also facing growing pressure to transform their business models for a net zero world while hitting increasing production and refining KPIs to meet growing global energy demand.
Those companies that wish to maintain competitive advantage for the long haul must continuously drive to improve refining margins, optimize well efficiency, automate repetitive manual processes, and reduce operating risks even when the cash coffers are full.
Operational excellence has proven to be an effective way to improve company processes, reduce operational and environmental risks, and drive business performance.
But operational excellence cannot be just a series of initiatives or spot improvements. For those companies that wish to truly drive operational excellence, it must be embedded into daily business operations and supported from the top. That means it must be instilled in the mindset and behaviors of all employees.
Three major oil companies - Chevron, ExxonMobil, and Marathon Petroleum – have made operational excellence a key pillar of their business and have a systematic approach to driving operational excellence. Here is a closer look at what that looks like at each of the companies.
Chevron
Chevron’s Operational Excellence Management program has been running since 2004 and focuses on enhancing worker health and safety, reducing environmental risks, improving processes, and increasing efficiency, reliability, and integrity.
Taking a cue from Toyota, the company has created what it calls the “Chevron Way.”
“Our Chevron Way values guide our actions and underpin strong OE performance that is fundamental to our company’s success,” writes Chevron CEO and Chairman of the Board Mike Wirth.
The Chevron way focuses on “getting results the right way,” according to the company website.
It is an approach underpinned by operational excellence and aims to ensure that workers are not taking shortcuts that might undermine the integrity of its operations. It also means that all staff are equipped with the knowledge, training, practices, and information they need to undertake their jobs safely.
The objectives of Chevron’s OEMS include reducing workplace fatalities and serious injuries or illnesses, eliminate high-risk process safety events, better manage environmental impact (including reducing resource usage), and address other business and operational risks.
Process standardization and optimization is a critical component of operational excellence. Chevron has a standardized five-component model to ensure that processes are simply and clearly written and integrated into practical work instructions and training to ensure that the workforce successfully practices them.
For instance, Chevron says that it focuses on maintaining the “integrity of equipment, structures and protection devices for the prevention and mitigation of potential incidents.” To achieve this, the company analyzes potential failure modes and effects and conducts regular inspections and testing.
Similarly, the company maintains standard procedures for vital functions such as the management of wells to reduce risk and ensure smooth operation.
“Assuring critical safeguards are in place before starting a high-risk task is an important step in prioritizing safety, so I coach employees and contractors to assess their work using standardized protocols before they begin,” said Olukayode Alade Verification and Validation Coach, Business Services Department at Chevron in a write up.
Lean and Six Sigma process improvement models are incorporated into the company’s OEMS to identify and improve key operational processes.
READ: Closing The Execution Gap: An Interview With Former Chevron President Ray Wilcox
ExxonMobil
ExxonMobil has an approach to operational excellence that it calls its Operations Integrity Management System (OIMS).
The OIMS framework has a set of 11 elements that includes leadership, risk management, design, maintenance, training, and operating assets. These elements set out clear expectations around behaviors and actions that both leaders and workers must take to reduce risk, ensure continuity of operations, and continually drive performance in the business.
“ExxonMobil’s OIMS Framework establishes common worldwide expectations to address the risks inherent to our business. ExxonMobil uses the term Operations Integrity (OI) to address all aspects of its business impacting personnel and process safety, security, health, and environmental performance,” the company states on its website.
One of the key elements of ExxonMobil’s framework is the expectation that the company will learn from “operating experience and incidents.” The company uses root cause analysis to understand why an incident has occurred and encourages lessons to be learned and shared across the company.
The company has also continued to evolve its business operations to drive better performance and efficiency. The OIMS is expected to operate in every division or business unit, “consistent with the risk inherent in the business.”
Breaking down traditional business silos is another thing that can help to drive process improvement and operations excellence.
In an earnings call earlier this year, ExxonMobil CEO Darren Woods cited how bringing experts together from across the business had brought dramatic improvements in process safety in the past few years. The company is now applying that approach to tackle new challenges in maintenance and technology to improve performance and efficiency, and reduce costs.
"The savings that we see going forward are really the result of a lot of different things being applied across a huge scale of our operations to significantly reduce cost,” he explained. “We open the doors between the different businesses across our corporation, take the best that each has to offer, bring those together and come up with an answer that's better than any one on its own."
READ: ExxonMobil Case Study: Overcoming Risk Assessment Challenges In The Oil & Gas Industry
Marathon Petroleum
As with both Chevron and ExxonMobil, Marathon has created a systemic approach to managing operational excellence. They call it their Operational Excellence Management System (OEMS).
In 2019, the company moved to a more integrated OEMS (from their previous approach, the RC14001® management system), which meant an increased focus on continuous improvement not just on following standards and compliance.
“Achieving operational excellence requires a clear understanding of business goals, an environment of trust and the opportunity to grow and realize our own potential. Our Operational Excellence Management System (OEMS) provides a systemic approach to advancing performance by outlining requirements that will enable us to achieve our goals and ensure our long-term success,” explains the company on its website.
The company says that a cycle of “Plan-Do-Check-Act” (PDCA) is at the heart of the management system. The cycle applies an iterative approach to ensure that processes are followed and continuously improved.
Additionally, all employees are encouraged to submit ideas for improvement.
“As our most valuable resource, our people are at the forefront of driving continual improvements that maximize value creation, enhance our nimbleness and resiliency, and improve our cost discipline – while never compromising our commitment to safety, environmental stewardship and operational excellence,” writes Marathon President & CEO Michael Hennigan.
“Our OEMS provides a framework to improve our performance and enables MPC and MPLX to achieve our goals and ensure long-term success.”
The approach has yielded enormous financial results, according to the company’s 2021 annual financial report. The effort to embed a low-cost culture across the company yielded $1.5 billion in structural cost reductions in 2021. The company attributed the lion’s share of the savings to reduced operating costs in its refining segment after they were able to reduce costs from $6 per barrel to $5 per barrel.
Other savings were made in corporate costs and efficiencies at MPLX, a midstream service provider.
Interested in learning more about this topic?
The Operational Excellence in Oil & Gas Summit is the most inspiring showcase of oil and gas industry innovation in North America. Now in its 13th year, the summit brings together over 300 senior level executives to share use cases and showcase trailblazing technologies that will transform your operations. Hear from industry titans like Shell, Equinor, Chevron, Delek and more during must-see keynote speeches. Download the agenda for more information.