From our Archives: A Look Back at the World's First Commercial Biofuels Plant
Interview with Suncor’s Stephane Demers
Add bookmark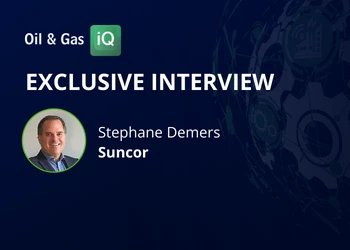
Oil and gas companies have a large role to play in helping the world meet its carbon targets. The production and extraction of oil and gas contributes approximately 9% to global carbon emissions with an additional 33% coming from customers burning the fuels, according to consultancy McKinsey.
But demand for oil and gas remains high. That’s why new technologies and decarbonizing oil and gas production will be hugely important to the world’s transition to Net Zero.
Canadian oil patch giant Suncor is among many oil and gas operators who have pledged support for Net Zero. Back in 2019, IX Network caught up with Stephane Demers to find out more about Suncor’s new biofuel facility – a plant that aims to produce ethanol from garbage. The plant was the world’s first commercial-scale biorefinery. Here's what he had to say at the time.
IX Network: Stephane, you have taken on a new role with Suncor as General Manager of Enerkem Alberta Biofuel facility. Can you tell us more about this new position?
I started in this new role in May 2019. I lead a team that operates the Enerkem Biofuel facility in Edmonton where Enerkem produces a waste-to-ethanol product in partnership with Suncor. They have a fantastic technology and with Suncor supporting the operations, we feel we’ve created a win-win partnership. Our main objective onsite is to combine Enerkem technology and culture with the Suncor culture and our operational experience to really improve safety, productivity, efficiency.
This Enerkem Alberta Biofuels facility is the first commercial-scale biorefinery.
IX Network: Could you tell us a little bit more about the facility and when it went into operation?
The facility started in 2015 as Enerkem Alberta Biofuels. It became the first of its kind globally to produce commercial-scale renewable methanol and it is now producing the ethanol from mixed municipal waste. We’re located onsite at Edmonton’s waste management facility.
Together, EAB and the City of Edmonton address the non-recyclable and non-compostable waste disposal challenge by diverting household waste destined to landfills. Partners with Enerkem at EAB, Suncor is interested in this kind of technology as an opportunity to diversify the mix that we have in our gasoline. Pending regulatory changes will require the percentage of ethanol in gasoline to increase so we’re trying to diversify as an oil and gas company and find new technologies to meet these future requirements.
Waste is normally in landfills, and so we divert waste from going to landfills and create added value by transforming it into ethanol. The capacity of the facility is really interesting. We’re still in that ramp-up period, and we did our first truck of ethanol at the end of 2019. That was the first big milestone for us onsite. The facility can process up to 100,000 dry tonnes of ultimate waste per year and produce close to 38 million litres of renewable ethanol.
IX Network: How is running a plant that is dedicated to creating renewable energy and diverting waste different than your previous experience in a petroleum refinery setting?
I would say that technology is technology. I was in a refinery plant in Montreal before – and am now running a facility with biofuel renewable technology, and in both environments, we started with operational discipline. We brought that kind of mindset into the EAB structure, talking to our people, doing the right thing, the right way every time.
To me there are three important components to this discipline: first of all, collaboration. It’s all about humans at the end of the day. You can leverage technology, but you need operators, maintenance staff and engineers to drive the effort. Collaboration was one of the big pieces of the pie that we tackled first, to make sure that we engaged our people, and created a culture of trust between Enerkem and Suncor.
Second – it’s important to bring a questioning attitude to understand the problem. When you commission something, you need to follow procedures and make sure that we adhere to them and instil accountability. As you are developing the technology, you’re not in that production mind-set and time flies by. Now that the facility is in operation, we’re bringing a more operational mind-set and putting safety and production first always.
The last one is really to continue to learn what is possible with this technology – seek the knowledge, the understanding, and ensure that the learning that we’re doing in Edmonton can be translated to other generations, and opportunities, in the future.
IX Network: You mentioned that new technologies are a key element. So given the emphasis on sustainability, are there any specific processes and technologies that are in use to reduce emissions and the plant’s overall carbon footprint?
Yes, definitely. When we talk about the Enerkem biofuel plant located in Edmonton, we’re talking starting from municipal solid waste and converting them into value-added liquid products. It’s really diversifying the energy mix, reducing greenhouse gas emission, making greener everyday products and offering a sustainable and circular economy that reduces the landfill.
When you look at the carbon index number, that technology uses a thermomechanical process that converts chemically recycled carbon molecules contained in the waste into added products: ethanol and methanol.
When you look at the low-carbon transportation biofuel by conversion index, it’s enough to fuel over 400,000 cars on a 5% ethanol blend. In turn, that biofuel reduces greenhouse gas emissions by around 60% compared to fossil fuel production and landfilling.
We know that all regulation will move in the next few years on the carbon index intensity. As a refiner, leveraging this technology helps us on our carbon index number.
For such a large-scale facility, this becomes particularly evident when you look at the impact on an annual basis. Compared to incineration, the conversion of 1 tonne of ultimate waste and non-recyclable plastics in the process can reduce GHG emissions by 600 kg of CO2eq, produce 745 L of ethanol and avoid the production of around 500 L of gasoline from crude oil. For a large-scale plant capacity of 134,000 tonnes of non recyclable plastics, the reduction of GHG emissions are evaluated at 85,000 tCO2eq/yr and 2,125,000 t over the lifetime of the plant (25 years).
IX Network: When setting up a new facility with all these new people, processes and technology, how do you go about incorporating operational excellence practices into it?
Operational excellence practices are key to our operations at EAB. As it’s a new facility we are making sure to really explain the “why” of operational excellence - actively listening to our frontline workers, creating a safe environment where they can exchange ideas, and are always seeing their leaders leading by example. We can have the best processes in the world and talk about operational excellence but, at the end of the day, you need to lead by example and show the way.
The other thing that we brought is to keep things simple and fit for purpose. Coming from a big organisation like Suncor, we have our process safety model and operational excellence model - big processes for a big company. We need to use this and apply it to this smaller facility – which is what I mean by fit for purpose.
IX Network: This plant is expected to reduce Alberta’s CO2 footprint by more than 1 million tonnes over its next 25 years of operation. What does a project like this mean for Canada’s energy industry as a whole?
There is a CO2 footprint that will be reduced, but it’ll also impact landfills in a positive way – we don’t have any place to put our garbage anymore, and by converting our garbage torenewable chemicals and biofuels, we are able to reduce our need for landfill space. When you’re able to use that waste that’s supposed to be landfill and extract that and convert that into the biofuel, ethanol, in parallel, you reduce your CO2 footprint. That renewable chemical and fuel, at the end of the day, is a lower CO2 footprint and reduces the GHG.
If we’re able to expand across Canada – think of the impact.
People sometimes look at me when I tell them what we’re doing, and they’re a little sceptical. When they come onsite and visit and we show them the little fluff that we get from the city and the clear ethanol bottle sitting just beside that fluffy garbage – they are fascinated.
IX Network: Can you explain in laymans terms how you are turning garbage into ethanol?
Yes. It is a “simple” 4 step process. Located in the city’s main landfill site, we are really close to the waste sorting facility in Edmonton, who receives the municipal garbage. The city sorts the recyclables and the compostable from the ultimate waste and does the shrinking. They dry the garbage and turn it into what we call a fluff. Then it comes on our site by a conveyor belt and we’re able to feed that fluff into a low-oxygen gasifier that transforms garbage and plastic though thermal oxidation.
What’s generated from that gasification process is a syngas. We’re able to clean the gas, remove contaminants, for example H2S. We have the technology to convert that first as methanol and sell the methanol.
When we have methanol, we have another process that brings that to another intermediate product called methyl acetate. From there we have another island that we call the ethanol island, which allows us to convert that into ethanol.
IX Network: What are the next steps for you as you continue to strive for sustainability?
Our next milestone is to increase production. Enerkem is continuing to develop the technology around the globe and is focusing on addressing three pressing global challenges. The first is to address the unsustainability of conventional waste management; the second is the growing demand for diversified resources; and the third is to reduce dependence on fossil sources.
Enerkem are already working on projects in Europe, partnering with industry to really meet local waste diversification objectives. The big picture is to roll out more projects across Canada over the next few years and help make Canada set a new global standard in waste management and renewable fuels.
Download the original interview here.