Three Areas Where Digital has Radically Transformed Operations at Flint Hills
Add bookmark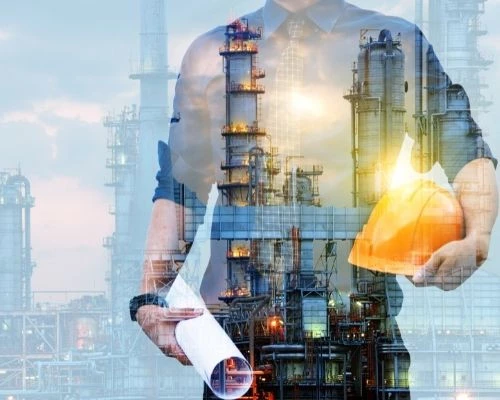
One of the reasons locals call Flint Hills Resources Corpus Christi refineries the ‘Emerald City’ is because its facilities are so big and bright, according to the company’s press office.
The operations, based in southern Texas, process more than 340,000 barrels of oil a day and produce a variety of products including jet fuel, gasoline, diesel, and the petrochemicals used in carpets, clothing, and tires.
But it’s not just the physical brightness of the refineries that make it stand out. Rather, the incredible assortment of digital platforms that it has incorporated into its operations set this refinery apart.
Brook Vickery, Vice President & Manufacturing Manager at Flint Hills Resources shared the company’s digital strategy at our recent Connected Worker event (you can watch the full video of his presentation here).
He describes how the company has leveraged cutting edge, connected worker technology to radically transform operations in engineering design, construction and maintenance.
Here’s how.
#1. Engineering Design
When the engineering team is planning a large turnaround or maintenance event, one of the applications that they turn to at Flint Hills is Matterport.
This application, originally developed for the real estate industry, allows for a 3D scan of the work site giving engineers a digital representation of the facility - a boost for productivity and an essential aid during COVID as i a tool for virtual walk throughs. It can also help capture dimensions so that engineers understand distances between points, further aiding in the planning process.
Another application, BlueBeam, lets the team collaborate on engineering drawings. The application allows for online mark ups, tracking who edited what and when. This enhances knowledge flow so that everyone can see in real time any proposed changes.
That means you don’t get into a situation where different engineers propose contradictory amendments, explains Vickery. Additionally, he says, you can pull in photographs and look virtually at the drawing and compare it to the actual site.
Finally, the company uses 3D modelling for project visualization. Many different teams, including field workers, use the 3D models. Vickery cites an example where they had a 3D model on site and the workers were able to look at the model and understand what was happening underground to better understand how to carry out the work.
#2. Construction
To monitor turnarounds, the company uses ProCore's construction management software. The application digitizes documents to support workflow and monitors job progress in real time.
For instance, when doing a turnaround, the crafts will pull a valve and scan a QR code. That scan progresses the job in real time, explains Vickery, and “automatically updates the schedule we have on big TVs in what we call the war room.”
It “allows you, as a leader, to see where the constraints are in your work,” he adds.
As the job nears completion, the application manages the “punch list” – the list of small tasks that need to get done in order to complete the job. Punch lists, according to Vickery, used to be manual and difficult to communicate but with ProCore the process is easier; the crafts can take a picture of the deficiency and incorporate it into the punch list allowing planners a better understanding of the tools, time and resources required to complete the item.
#3. Field Maintenance
One of the keys principles of Lean Management, a widely used philosophy for creating efficient business operations, is to make work visible to all the team members.
Kanban boards, where companies track tasks and their status, are one way to ensure that all team members understand what needs to be done and keep track of progress.
Vickery describes how the company has moved from printing out work orders on sticky notes to a fully digital management system, Lean Kit.
“All of our operators were empowered with Lean Kit,” he explains. “For instance, when the crafts completed a job, they could go to the mobile interface and move the job to complete. That updates in real time for everyone.”
Mobile platforms are another area where field workers are coming up with innovative new ways to use the technology.
“Once we got iphones into the hands of all the operators they quickly figured out how to apply them in very unique ways and came up with applications that we never envisioned,” observes Vickery.
For instance, the operators need to track how the levels in site glasses are changing over time. According to Vickery the operators quickly figured out how to use apps to enter the measurements and track drawdowns in the vessels.
Another example of creative innovation by operators saw one employee purchasing an infrared camera attachment to help figure out the location of a blockage in a steam track. The operator bought the camera – something you can purchase at most electronics retailers – and attached it to the iPhone. That transformed the iPhone into an infrared camera that could provide thermal imaging of the object to help to identify the blockage.
Finally, the company has deployed a digital platform for maintenance procedures. Multiple people can see the document at the same time, versions are tracked automatically, and operators are able to embed videos of critical procedures - such as “this is what I mean by turn it slowly” – to reduce operating errors and ensure essential knowledge is passed on effectively. At the time of his presentation, the company had already digitized around 700 procedures.
In order to make these digital field operations a reality there are some practical infrastructure concerns that need to be addressed. Vickery says that you need to ensure that there is site wide WIFI or cellular data available and that the bandwidth is adequate to support your operations.
“All our craftsman - all our operators - have a cell phone or tablet and that becomes part of the infrastructure,” he says adding that “there’s an incredible amount of data that starts to flow and you have to make sure that the pipeline works all the way from the field through to network systems all the way to the cloud and be available for all the different aspects.”
As many of the areas where these digital platforms and devices are used are classified as hazardous areas, the team had to do a lot of work early on to understand which devices would be acceptable under what circumstances. After extensive testing, the appropriate devices were found that met the criteria.
There is also the people side of the equation. At Flint Hills, they have an operations transformation team that acts as an interface between the operators and the IT teams. Their job is to ensure that any new software works at the operator level, to troubleshoot the inevitable glitches, and to vet new apps that operators propose using.
Vickery says that listening to the operators and understanding their challenges is critical to the success of the program.
“Always start with the ‘Why’? Why are we doing this? Why is it important? How will we benefit?”
It’s important not to pursue technology because “it’s cool,” he cautions. “Pursue them because they’re going to make someone’s life better, they’re going to help with our productivity and they’re going to create value.”
Learn more about leveraging connected worker technology and building a connected workforce to improve operational efficiency, training, asset management, quality, and safety at The Connected Worker Summit.