Choosing the Right Connectivity: Connected Worker Initiatives at Chevron
Add bookmark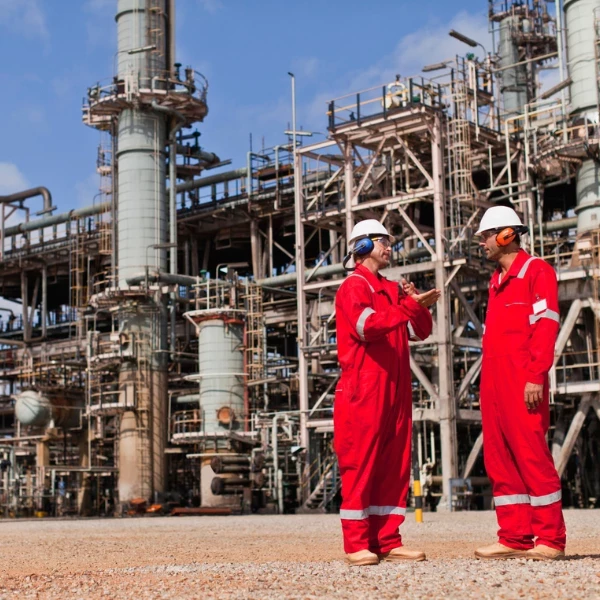
As oil and gas leaders look to gain competitive advantage and maximize market share amidst an evolving energy landscape, the value of connectivity – the “Connected Worker” is more important than ever as a key enabler of operational efficiencies, training, upskilling and, most importantly, keeping the workforce safe.
Chevron is a global energy company based in the United States and is at the forefront of implementing innovative technologies that facilitate enhanced safety, productivity, and connectivity. As an integrated energy company, Chevron’s operations span exploration, production, refining, marketing, distribution of energy products, and exploring the promise of future energy sources. Across its operations, the power of connectivity and the Connected Worker helps safeguard Chevron’s workforce.
“Safety is a critical consideration, and we always design our network infrastructure with two layers of broadband connectivity,” says Ted Stoves, Product Owner – Connected Worker Group, Chevron.
Please join the ‘Infrastructure and Connectivity to Support Connected Worker Project Roll-Out’ at the Connected Worker Summit in Munich, from 4-6 December where Ted joins us for an exclusive interview to talk about Chevron’s leadership in enabling the Connected Worker. He will share key insights and lessons learned in safely deploying connectivity solutions in potentially hazardous environments.
Maryam Irfan, IQPC: As Product Owner of the Connected Worker Group at Chevron, how are you supporting the Connected Worker project roll out?
Ted Stoves: Connected Worker sits within the operational technology product line at Chevron. We work with several strategic partners to achieve our objectives across various capabilities, including:
RTLS (Real-Time Location Services)
PTToB (Push-to-Talk over Broadband) or IP 2-Way radio.
Wearables like smartwatches
Workforce safety metrics
Free bone conduction headsets for mobile workers
We also focus on meeting smart device requirements in hazardous areas to ensure the safety of the workforce. Additionally, we are introducing augmented, mixed, and virtual reality applications to assist the operational workforce with training and collaborative engagement, leveraging digital twin technology.
Many of these areas are still evolving. Some are in the conceptual phase, while others are deployed as pilots. A few have already transitioned into production and are currently in operational use today as we scale what is working across to other assets.
READ: EIT Manufacturing on Paving the Way for Future Proof Industry in Europe
Maryam Irfan, IQPC: What connectivity and infrastructure factors should operators consider when implementing a project like this?
Ted Stoves: In the oil and gas industry, we face several unique challenges. First, we have dense industrial infrastructure which creates a challenging RF (Radio Frequency) environment for wireless connectivity. Second, we require hardware that adheres to hazardous area classification levels, determined by their geographic location. This means that our range of products is limited and often more expensive.
Implementing infrastructure projects requires meticulous planning of operational activities without impacting current production.
We must also make strategic decisions regarding data hosting. We need to determine whether to store data on-premises, in a client's cloud, or in Chevron's own Azure Data Lake. We also choose our connectivity methods by deciding whether to leverage existing commercial LTE services, invest in private LTE, enhance our industrial Wi-Fi infrastructure, or adopt technologies like Bluetooth Low Energy or Ultra-Wideband for improved accuracy.
Maryam Irfan, IQPC: When choosing between Private LTE and Wi-Fi for connectivity, what are the potential advantages and disadvantages?
Ted Stoves: The performance of LTE depends on the frequency licenses obtained and the output power of your E or G node B. Private LTE can be expensive in terms of infrastructure and deployment but can offer extensive coverage if you obtain low-band licenses in the 800 MHz range.
On the other hand, 802.11ax Wi-Fi deployment can incorporate BLE (Bluetooth Low Energy) multi- radio components in the same form factor, providing improved accuracy. The density of a Wi-Fi deployment can also offer increased capacity, leading to improved throughput speeds and an enhanced user experience.
Striking the right balance between cost and deployment requirements is crucial to ensuring that broadband availability is neither over-engineered nor under-engineered.
Maryam Irfan, IQPC: Certain areas of the facility may have unique connectivity requirements, especially areas with high density of equipment, how can one address this?
Ted Stoves: Deploying spread spectrum technologies like LoRaWAN can alleviate hardware requirements due to the pervasive nature of the coverage at that frequency. LoRaWAN is especially helpful when trying to utilize sensors within dense industrial environments where higher-band spectrum options like Wi-Fi might prove less reliable.
In addition, some private LTE bands or narrowband IoT technologies rely on existing LTE capacity, often in the gigahertz range.
LoRaWAN deployment requires a different design approach and a portfolio of components that are LoRa-capable. Addressing specific coverage requirements, be it for LoRa or LTE, during the design phase is paramount to ensuring success when deploying technologies that rely on broadband or narrowband availability.
WATCH: Scaling the Adoption of Generative AI Across Enterprises
Maryam Irfan, IQPC: Are any failover mechanisms put in place to ensure continuous connectivity in case of network outages or equipment failures?
Ted Stoves: Safety is the highest priority in our operations, and we always design our network infrastructure with two layers of broadband connectivity. In most scenarios, industrial Wi-Fi provides our primary layer of connectivity, with private or commercial LTE serving as a backup. In jurisdictions that permit ground stations, we also deploy Starlink for backhaul.
Depending on the specific network environment, the order of our broadband layers can be reversed. For instance, LTE may become the primary layer in remote areas where comprehensive Wi-Fi coverage is lacking. This shift can lead to an 8-12-second period of downtime as devices and mobile sensors re-register onto the new network layer. Teams should mitigate any safety concerns this might cause in some situations.
Maryam Irfan, IQPC: Do you have any successes or lessons learned through this project that you can share?
Ted Stoves: Some of the biggest challenges when deploying Connected Worker technology revolve around broadband availability. Several of our business units have legacy Wi-Fi networks that were established prior to the advanced demand for augmented coverage that has come with increased innovation in the industry. Consequently, ad hoc design adjustments are required to ensure the successful deployment of systems like RTLS, PTToB, smart glasses, smartwatches, and the utilization of augmented, mixed, and virtual reality technologies.
Our current focus is prioritizing comprehensive foundational design to fully support our operational workforce, ensuring broadband connectivity in all areas to meet anticipated operational use cases.
LISTEN: Episode 3: GHGSat on the Importance of Remote Methane Monitoring
Maryam Irfan, IQPC: Lastly, what are you most looking forward to at this year’s Connected Worker Europe Summit?
Ted Stoves: I am eager to observe how other industries are approaching Connected Worker capabilities and sharing our learnings. Our industry’s commitment to worker and environmental safety demands distinct and unique requirements and forums like the Connected Worker Europe Summit can be good opportunities to share valuable insights that benefit us all as we continue to innovate.
Interested in learning more?
If you want to understand how to better connect your workforce to the digital resources they need to work more effectively and increase productivity across your manufacturing operations, then our Connected Worker Europe Summit is your must attend event of 2023.
Join over 150 of your peers in Munich to discuss What’s Next for Connected Worker in the Manufacturing 4.0 Operating Environment and learn to develop a holistic ecosystem of connected people, connected processes, connected technologies, and connected data. Download the agenda for more information.