Four Examples of Wearable Technology in Oil and Gas
Add bookmark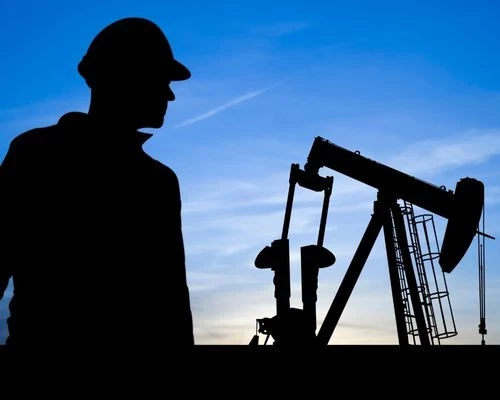
Industrial environments are increasingly becoming interconnected ecosystems. Data coming from sensors worn by workers or on machines is ever more connected to the internet and analyzed by software for monitoring purposes, trend analysis, operational alerts, and predictive risk identification.
Wearable technology – which includes helmets, eyeglasses, watches, “smart fabrics” or other devices that workers can wear – is a growing trend in the oil and gas sector to help keep workers safer, access information and support directly in the field, and conduct essential job functions more efficiently.
Wearable technology is of particular use in heavy industrial environments where workers are expected to work with their hands. Carrying extra equipment such as laptops, mobiles or tablets in addition to tools and protective clothing, is often more of a hindrance than a help. Wearable technology, such as watches and glasses, solves this problem by giving workers access to digital resources without increasing the amount of equipment they need to carry.
Here are four examples of how oil and gas companies are using wearable technology to drive improvements in their operations:
#1: Remote Worker Assistance
Tackling a difficult maintenance problem on a complex piece of machinery can be challenging for any worker. Workers often require specialist knowledge and support from technical experts.
TotalEnergies and Mitsubishi Chemicals are among the companies that have adopted a hands-free headset from RealWear that gives workers real-time access to MS Teams as they carry out maintenance operations in the field. The helmet connects workers with technical experts who may be located offsite. A video camera built into the headset gives the remote users a visual on what the worker is looking at to further aid in remote machine diagnosis.
“We can have specialists who are in different geographical locations in we can bring them together virtually where they can all see the same information and provide advice,” says Patrick Short, Digital Manager, Smart Factory, Mitsubishi Chemicals.
READ: How High-tech Helmets and Huddle Boards Drive Efficiency at TotalEnergies
#2: Safety
Getting workers home safely at the end of the day is one of the top aims for oil and gas companies. The oil and gas industry is full of hazardous situations and environments.
Wearable technology can help fulfil a variety of safety functions: tracking worker locations, monitoring vital signs to mitigate risks in hazardous and/or remote locations, and improved access to information for field workers to alert them to possible dangers in their environments.
“If someone is working in extreme conditions – such as hot weather – or undertaking a particular task that might be stressful we want to understand how they are reacting to the environment to keep them safe,” says Anna Bainbridge, Digital Manager, People Engagement at Mitsubishi Chemicals.
READ: 6 Technologies Redefining How Energy Companies are Managing Worker Safety
#3: Immersive Training
Virtual and augmented reality headsets can offer an effective training environment for new recruits. As the oil and gas industry scales up production, older workers retire, and young people increasingly turn away from industrial jobs, it has become more difficult to find and retain workers. Tools such as VR/AR allows the industry enables the industry to more effectively train new workers and assist in greater knowledge retention.
Virtual reality simulations, for instance, give new recruits the experience of the real world from the safety of a training center.
Abu Dhabi National Oil Company (ADNOC) Gas Processing has been successfully using VR to reduce training costs and improve competency among its plant operators and maintenance personnel, according to the Journal of Petroleum Technology.
Augmented reality is another wearable device that offers potential for oil and gas companies. A wearable device, such as glasses, can help to overlay reality offering less experienced staff access to important visual guides, text, and other information that can help them carry out their jobs effectively and efficiently.
#4: Improved Customer Service
Wearable technology need not only be limited to workers operating within the company’s own operations. It can also be used to deliver more effective customer service.
For instance, Shell offers a service called the Shell Lube Advisor, which helps customers select the right lubrication methodology to improve machine performance, extend component life, and reduce maintenance costs. Traditionally, the service has required on site meetings between technical experts at Shell and their customers.
Earlier this year, however, Shell integrated wearable technology into this service for customers in the Middle East. The service enables remote inspection and maintenance, eliminating the need for Shell experts to be deployed on site.
“The Lube Advisor integrated with wearable technology is the result of an accelerated product development by Shell to help customers overcome the limitations on face-to-face interactions in industrial environments and jobsites,” says Haytham Yehia, general manager, Shell Lubricants Middle East, quoted in Plant Machinery Vehicles.
“The use of wearables gives us a new opportunity to support our customers, remotely and in real time. By offering personalized, online consultation delivered via a wearable device, we eliminate the need for physical site visits by Shell experts. Lube Advisor, currently, encompasses all value-added services related to lubrication provided by Shell, and we’ve found this to be a reliable and efficient way to work with customers.”
Interested in Learning More About this Topic?
Join us at The Connected Worker Summit on March 28-30, 2023 and network with over 150 of your industry peers at the Norris Conference Center in Houston, TX., and learn how to evaluate the existing gaps in your connected worker capability and identify the data-driven solutions that will drive continuous improvement across your operations. Download the agenda for more information.