Implementing the ‘Digital Manufacturing Acceleration' Program at Danone
Add bookmark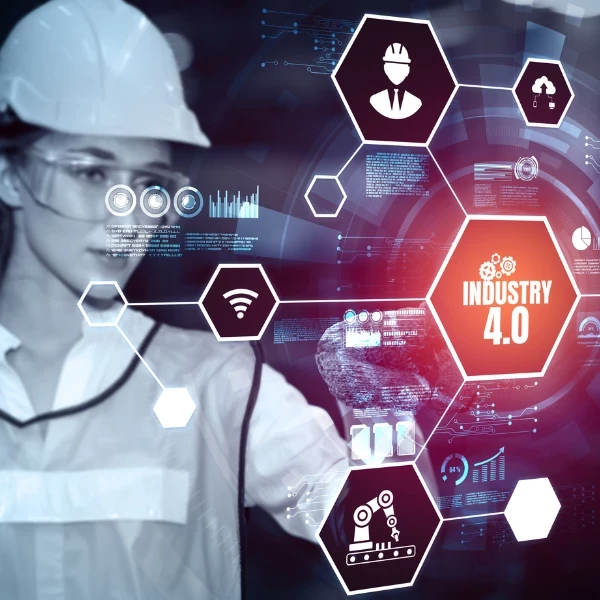
Danone, a leading multi-local food and beverage company building on health-focused and fast-growing categories in four businesses: Essential Dairy and Plant-Based Products, Waters, Early Life Nutrition and Medical Nutrition. With more than 100,000 employees, products sold in over 120 markets, and global operations, the group actively pilots and adopts digital solutions in line with industry trends and expectations.
In recent years, with the intention of increasing the phasing of digital transformation, the group adopted the Digital Manufacturing Acceleration Program (DMA), allowing them to evolve their operations ecosystem quickly and effectively.
As the Global Digital Manufacturing Senior Manager, German Figueroa has assumed a leading role in the implementation of the DMA across Danone’s operations. “This program is designed to help our factories accelerate the transition from Industry 3.0 to Industry 4.0, with the main goal of enhancing efficiency, flexibility, and resilience.”, German shares ahead of his closing keynote at the Connected Worker Europe Summit taking place in Munich from 4-6 December.
Read as we delve into the DMA’s intricacies, exploring the program’s critical components and its alignment with Danone’s broader digital transformation strategy.
Maryam Irfan, IQPC: As the Global Digital Manufacturing Senior Manager at Danone, what does your role entail?
German Figueroa: As part of the global team in charge of implementing digital manufacturing in Danone, I’m responsible for the team that manages the global catalogue of digital solutions which are central to Danone’s operations. Our goal is to maximize the catalogue’s usage, drive adoption and ensure satisfaction of the end users. We also ensure that the tools remain up to date and in line with the evolving needs of our factories so that everything runs smoothly.
READ: Choosing the Right Connectivity: Connected Worker Initiatives at Chevron
Essentially, this catalogue is organized within a framework we refer to as a digital compass which helps us extract value from Industry 4.0 technologies by mapping out use cases and tools for our factories. We position ‘tools’ at the end of this sequence because for us, tools play the role of ‘enablers’ for specific use cases. They are not a magic solution by themselves but rather an enabler that helps our factories implement use cases that drive enhancement in various aspects of our operations.
Maryam Irfan, IQPC: Can you give us an overview of the DMA at Danone?
German Figueroa: Our journey into the digital realm began several years ago. We initially started with the concept of lighthouses to test and gain a better understanding of technologies within the various pillars of Industry 4.0. As we grew confident in our approach, we initiated a program called ‘Digital Manufacturing Acceleration. This program is designed to help our factories accelerate the transition from Industry 3.0 to Industry 4.0, with the main goal of enhancing efficiency, flexibility, and resilience. To achieve this, we leverage new technologies to boost productivity.
Our program is very factory-centric, emphasizing a bottom-up approach with a focus on impactful use cases. We have a defined methodology that we roll out in waves across different regions. So far, we’ve successfully implemented the program in five waves across Europe and are in the process of rolling out three waves in North America. We’ve already covered Latin America and are extending our efforts to Asia, Oceania and beyond. We refrain from doing everything at the same time and focus more on methodology, people change and developing technical expertise.
Maryam Irfan, IQPC: What are the critical components of the DMA and how does it fit into the company's broader digital transformation strategy?
German Figueroa: The DMA is a program structured around what we refer to as a recipe made of three main ingredients: the Blue Stream, the Red Stream, and the Yellow Stream.
The Blue Stream is the project management team which focuses on identifying future use cases that will help factories identify and achieve specific targets. This stream assists in understanding which technologies can address pain points and boost productivity by reducing waste and more.
WATCH: Scaling the Adoption of Generative AI Across Enterprises
The Red Stream, known as the technical stream, is dedicated to standardizing and future-proofing technical solutions. This team ensures that the current architecture of the factory will allow them to implement new technologies in terms of service capacity, shop floor Wi-Fi, and cyber security. Cyber security is a crucial aspect to consider because as we transition from Industry 3.0 to 4.0, it opens our factories to the outside world. Therefore, it is essential that all factories follow robust cyber security standards.
Finally, we have the Yellow Stream, which is the most important one. It focuses on our people and how we help prepare our teams for future needs. It addresses skill development, change management and readiness, collaborating with local teams to prepare employees for new tools and technologies. The goal is to upskill the workforce and minimize social impact through effective change management.
Maryam Irfan, Oil & Gas IQ: What are you hoping to achieve with this program and what have been the challenges so far?
German Figueroa: One aspect of my job that I particularly appreciate is my role in simplifying the work for our operators. My aim is to minimize the complexity of their daily tasks while maximizing their overall experience. I do this by ensuring they no longer have to search for paper documents or question how to perform specific tasks.
Our Connected Worker programme is designed to boost operator experience through mobile and paperless workflows. It allows operators to manage up to 80-90% of their daily tasks though a single, user-friendly application.
This unification of workflows and the need to connect involves interactions with both established and new technologies. Interfaces, although they seem simple, are often quite complex. One of the challenges we face is connecting with systems like SAP, local systems, and PLCs on the production line. While we have a robust methodology to manage this, it remains an interesting challenge we continue to address.
Another crucial aspect is ensuring user adoption and participation in the design process. Operators and end-users need to be at the center of the design, actively involved in validation and feedback. They should be the ones guiding us by articulating their needs and preferences, helping us create tools that truly serve them.
LISTEN: From Data to Action: Monitoring Methane Emissions with Project Canary
Maryam Irfan, Oil & Gas IQ: How are you measuring the success of these efforts?
German Figueroa: For the DMA Program, we measure success through impact. Our ultimate goal is to maximize the impact of our factories, making them more flexible, increasing their output, improving efficiency by simplifying processes. So, the question is, how do we gauge its success? We have an impact tracking methodology where we meet with factories on a monthly basis to monitor each of their use cases. We assess how well they align with the initially defined impact objectives outlined in the business case.
To provide some context with numbers, we've achieved great success by implementing DMA in over 50 factories worldwide, spanning regions such as Europe, North America, the Middle East, Asia, and more. Among these factories we've already identify a pipeline of productivity - of which 60% is already in execution phase. This means that, in the next five to seven years, we anticipate seeing a substantial transformation of this potential productivity into actual results.
Maryam Irfan, Oil & Gas IQ: What are you most looking forward to at this year’s Connected Worker Chicago Summit?
German Figueroa: I am looking forward to hearing what our peers and other big companies are doing around this concept because for me, Connected Worker is at the centre of digital transformation. This is the tool that really impacts operators and enables them to improve, and so I am interested to hear what others are doing and to learn from their experiences and strategies.
Interested in learning more?
German Figueroa will be talking more about the ‘Digital Manufacturing Acceleration' Program at The Connected Worker Europe Summit this December. If you want to understand how to better connect your workforce to the digital resources they need to work more effectively and increase productivity across your manufacturing operations, then our Connected Worker Europe Summit is your must attend event of 2023.
Join over 150 of your peers in Munich to discuss what’s next for Connected Worker in the Manufacturing 4.0 Operating Environment and learn to develop a holistic ecosystem of connected people, connected processes, connected technologies, and connected data. Download the agenda for more information.