Covid-19’s impact on digital transformation in upstream oil and gas
OSIsoft’s Cindy Crow says oil and gas companies need to improve their agility and adopt a market-proven approach to drive immediate business impacts during the current global pandemic
Add bookmark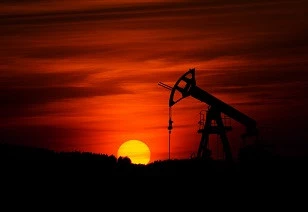
Coronavirus has had a huge effect on global oil demand and prices causing WTI/Brent crude oil benchmarks to plummet. Low prices and an unprecedented drop in demand has created difficulties for the upstream sector in the near term, especially in regions which have unfavorable production economics.
The debt-ridden US shale/tight oil industry is likely to witness the biggest hit, with operations curtailed as drilling capital budgets are cut and production declines in a historically low-price environment.
In order to remain competitive during the pandemic-driven downturn, upstream oil and gas companies have to leverage digital transformation technologies that can deliver a broad, rapid impact on their bottom line.
Not all Industrial IoT (IIoT) solutions are practical in the face of disruption, however. This is no time for investing in hyped software promising results without marketplace validation. Crises call for agility, not experimentation, and require a market-proven approach that can drive immediate business impacts.
Operational data is the answer
As top-line growth shrinks during this period, oil and gas producers will be forced to fight for every dollar in bottom-line savings. The answer is to adopt real-time operational intelligence that can offer a dramatic impact on both OpEx and CapEx.
For 40 years, OSIsoft has delivered a real-time data infrastructure that gathers operations intelligence at any scale and transforms it into actionable insights that directly impact the bottom line of oil and gas operators. We have hundreds of success stories presented by customers – including 85 per cent of top oil and gas companies – about solving the toughest of operational challenges in good times and in bad.
Chevron, Shell, Saudi Aramco, Petronas and other leading energy companies rely on OSIsoft’s PI System for operational excellence, predictive maintenance, asset reliability and energy optimization.
Devon Energy uses the PI System in their WellCon facility’s integrated operations center to get real-time drilling, completion and operating results to key decision-makers. Leveraging contextualized operational data, Devon’s engineers can gain real-time visibility into their wells to drive efficiency. The ability to improve decision-making with operational data enabled the company to achieve multi-disciplinary collaboration throughout the drilling and completions process.
Devon used the WellCon facility for rotary trend analysis to help land the drill bit more consistently. The PI System now enables WellCon to measure the exact deviation, driving future improvements and huge cost savings. The system also reveals granular information, such as the rotary RPMs, hookload, depth of cut and weight on bit on a dashboard with KPIs.
Relying on real-time operational data, Apache has created their Remote Operations Center (ROC) to increase operational visibility of field staff, reduce downtime and minimize “windshield time” spent by personnel driving to remote locations by being able to predict issues before they occur.
With the PI System delivering real-time intelligence to the ROC, Apache’s field personnel no longer need to conduct operator routes and can drive only to those wells that require their attention based on asset data. Crews can view critical asset information on an ESRI map that shows all of their vehicles, allowing them to contact the field worker who is closest to the well. The system has saved Apache significant amounts of time, miles, money and improved safety, as well as drilling, completions and production performance.
All the pieces needed to solve problems with operations can be optimized and safety improved with a real-time data infrastructure that gathers, contextualizes and analyzes operational data. The PI System can capture key drilling events, stick-slip and associated critical attributes such as rate of penetration as well as key calculations such as drill string volume. In addition, the visualization of multiple wells and drilling, completion or production progress gives engineers a complete view into all variabilities and metadata of the well.
Real-time analytics empower operators to make decisions that significantly affect financial performance. Leveraging operational data, operators can prioritize which wells to bring back online, which to remain shut-in and which to perform maintenance on.
During the current Covid-19 pandemic, the PI System has been critical in remotely monitoring of drilling and production operations, allowing engineers to have a 360-degree view of their equipment – even when they need to work from home. Operations personnel and engineering have real-time insight into the operations to enable them to make data-driven decisions necessary to open or close in wells and keep tanks from overflowing while ensuring the health and safety of personnel.
The pandemic may be forcing the oil and gas industry to rethink its business models, but as with any crisis, new possibilities arise. The gap between companies leading the charge with digital transformation and the laggards is now growing exponentially. Some companies will not be able to find the means to withstand the incoming tide. Others will view it as an opportunity to transform their organization and come out stronger than ever.
Find out how the PI System can optimize drilling and production operations by clicking here.